The aerospace industry is continually seeking lighter, stronger, and more efficient planes. As a result, materials used to construct aircraft have advanced significantly. From aluminum to high-end composites, and now 3D-printed components, the history of material development is one of performance, sustainability, and engineering brilliance.
From Aluminum to Composites: Why the Shift?
Aluminum has been the staple of aircraft construction for decades since it is not heavy and can withstand corrosion. However, greater fuel economy and lower emissions have compelled the industry to look for composite materials.
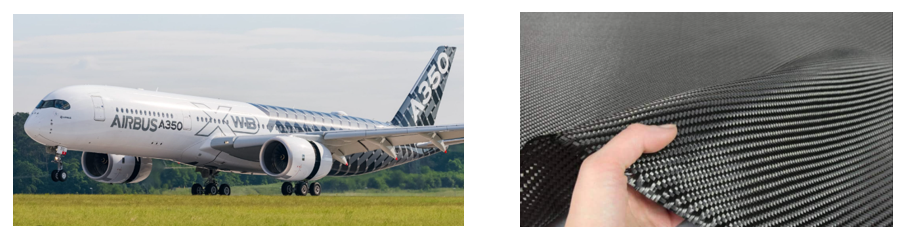
Take the Airbus A350, for example: its structure is comprised of over 50% composites such as carbon fiber-reinforced polymers. These offer a higher strength-to-weight ratio than metallic materials, allowing for considerable weight savings—directly translated to fuel efficiency and enhanced ranges.
In addition, composites are corrosion- and fatigue-resistant, significantly extending the life of aircraft structures. But it also has disadvantages: higher production costs, complicated production techniques, and non-fire-resistant (they release toxic fumes when they burn) still hinder them from being implemented universally.
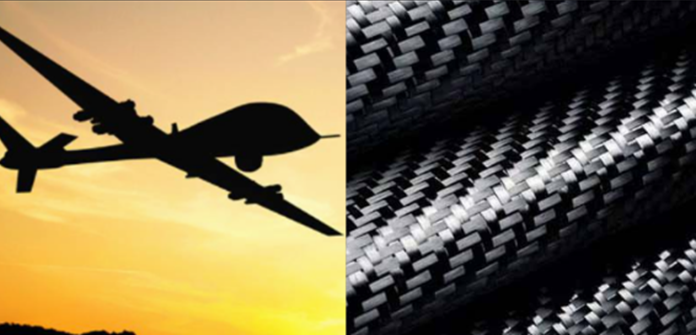
3D Printing’s Role in Material Evolution
3D printing, or additive manufacturing, is transforming how aerospace parts are designed and built at a rapid rate that is alarming. It helps engineers design complex geometries which are impossible with traditional manufacturing methods while simultaneously reducing material wastage.
For instance, aerospace companies using high-performance 3D printers (e.g., the Roboze ARGO 500) have realized up to 28% weight reduction in structural components. Personalization, fast prototyping, and localized part production (especially for rare or replacement parts) are also notable benefits.
But 3D printing is not without its drawbacks. Not all things can be 3D printed, and some mechanical properties can be variable as a function of print orientation or environmental conditions of fabrication. But all that being said, it’s an area of sustained development, with certifications and material standards improving year by year.
Conclusion
Aircraft materials have not only developed out of technological interest, but also because they had to. The need for lighter, greener, and more capable aircraft has driven composite materials and 3D printing to the center of the future of aerospace engineering.
As these technologies continue to evolve, we’re likely to see even more radical shifts in how aircraft are built, perhaps with entirely printed wings, morphing surfaces, or new heat-resistant composite alloys ready for space travel.
Sources:
– Airbus – Aviation’s Material Evolution
– Roboze – 3D Printing for Aerospace: Advantages and Applications
– Xometry – 3D Printing in Aerospace: Materials and Classifications